Top 5 Qualities of a Trusted Rubber Roller Manufacturer
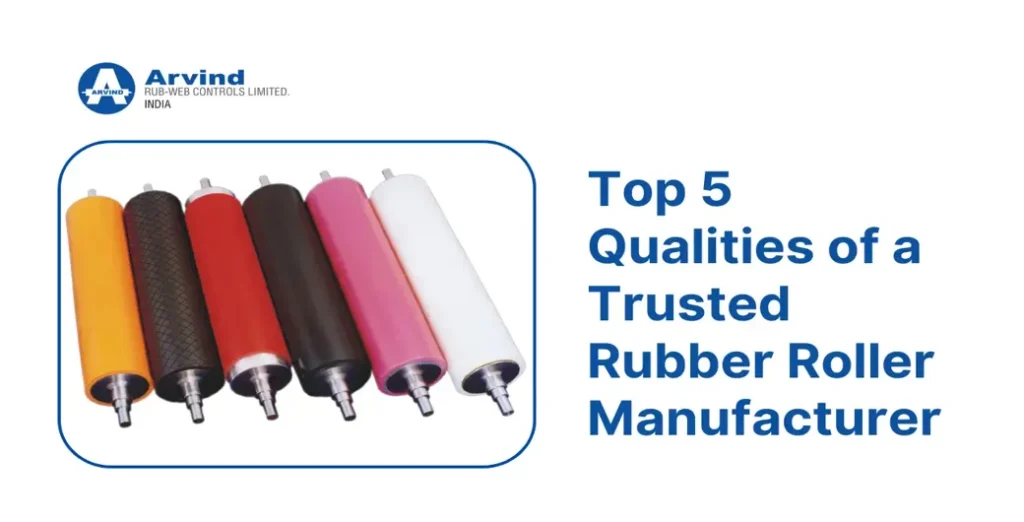
Rubber rollers are important components in industries like printing, textiles, packaging, steel, and more. From accurate web handling to ensuring a flawless finish, the quality of these rollers directly impacts productivity and product quality. But how do you choose the right partner among the many Rubber Roller Manufacturers ? Partner with us to deliver advanced technology rubber roller solutions designed for longer lifespan, performance, and follow global standards. Key Qualities to Look for in a Rubber Roller Manufacturer Proven Industry Experience Experience speaks volumes when it comes to selecting an Industrial Rubber Roller Manufacturer. Companies with years in the industry understand the different challenges of multiple applications and offer solutions customised to meet specific production needs. Use of High-Quality Materials High-quality raw materials ensure rollers resist wear, maintain accuracy, and perform consistently under high-speed and high-volume operations. Trusted manufacturers select compounds and core materials based on your application, be it heat resistance, anti-static properties, or chemical compatibility. Advanced Manufacturing Technology Leading manufacturers use advanced machinery, dynamic balancing systems, and strict quality controls to produce rollers with perfect concentricity and remove hardness. This ensures smooth operations and low vibration in your machines. Looking for an expert rubber roller supplier & exporter company in India? Arvind Rub-Web Controls Ltd. offers customized rollers built to meet international standards and your industry needs. Inquiry Now Customization Capabilities Not every process requires the same roller. A trustworthy supplier provides custom designs, sizes, and coatings to match your operational requirements, ensuring maximum compatibility with your existing machinery. Complete Support Services Beyond production, a trusted manufacturer offers installation guidance, maintenance support, and after-sales full service, helping you extend the lifespan of your rollers and reduce downtime. Conclusion Choosing the right Rubber Roller Manufacturers is an investment in your plant’s performance, safety, and product quality. With the right partner, you get trust, longer lifespan service, and high-performance solutions for every application. Trust Arvind Rub-Web Controls Ltd., a leading rubber roller supplier & exporter company in India, for accurate high quality rollers that drive operational quality.Rubber Roller Manufacturers
Why Quality Matters When Buying Industrial Rollers
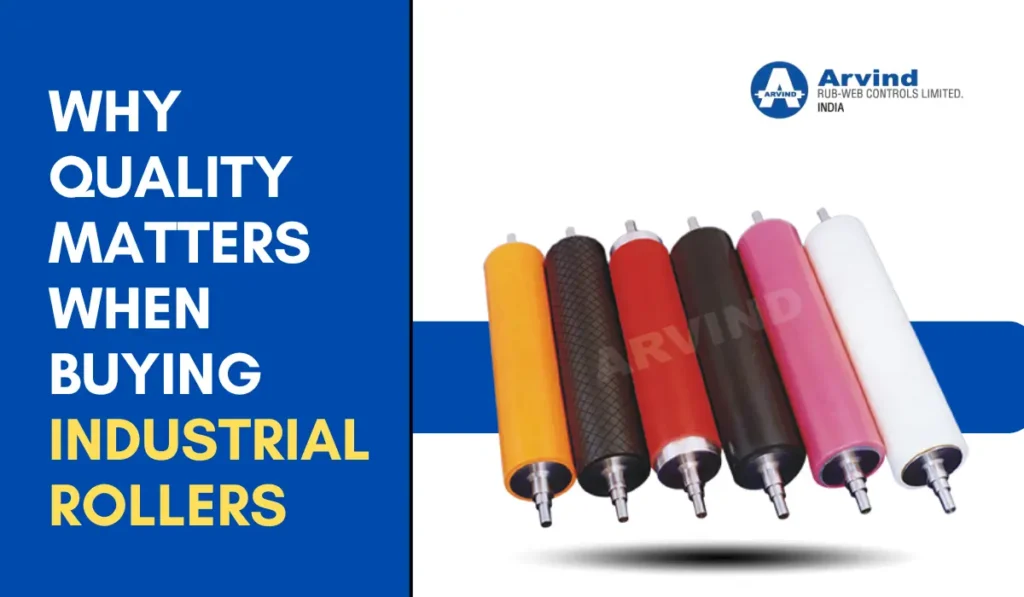
In manufacturing, every component plays a vital role in maintaining smooth and efficient operations. Among these, industrial rollers are the silent heroes that keep processes running smoothly across industries like printing, packaging, textiles, steel, and more. Whether it’s for conveying, laminating, embossing, or coating, high-quality rollers are essential for delivering consistent results. That’s why choosing a reliable Industrial Roller Company isn’t just a purchase it’s a strategic investment in the long-term performance of your production line. At Arvind Rub-Web Controls Ltd, we specialize in expertly manufactured rubber rollers that power up your productivity with performance. What Makes a High-Quality Industrial Roller? Industrial rollers are the humble machine components that operate tirelessly day after day. When manufactured with accuracy and from high-grade & high quality materials it required well experience person to design the rubber compositions which Arvind Rub-Web Controls Ltd company do last 40 years, they offer long-lasting performance and reduce downtime. Arvind Rub-Web Controls Ltd has very well knowledge for each application of the roller so we can design the composition accordingly which gives long lasting performance. A trustworthy Industrial Rubber Roller Manufacturer knows that industrial environments are demanding. Machines operate under high speeds, extreme temperatures, and rigorous cycles. Rollers that can’t keep up with these conditions will inevitably fail, leading to costly delays and compromised product quality. Quality Means Consistency One of the most key factors in any production process is consistency. Low-quality rollers often have issues like unbalanced weight, uneven surfaces, or inconsistent coatings, leading to misalignment, poor print registration, and inferior finishing quality. When you choose to work with an experienced Rubber Roller Company, you ensure uniformity in texture, hardness, and diameter, all of which are vital for maintaining output quality. Whether it’s printing paper, embossing fabric, or applying adhesive coatings, industrial rollers must consistently deliver precise, repeatable results with every batch. That level of consistency only comes with quality engineering and rigorous quality checks, which established Rubber Roller Manufacturers follow to as a standard practice. Why Material Quality Matters Industrial rollers are made from various materials including rubber, silicone, polyurethane, and steel. The quality of these materials determines how well the roller can resist chemical exposure, heat, abrasion, and pressure. Using subpar materials to cut costs may work short term, but it inevitably leads to faster wear and higher maintenance costs. A high-quality Industrial Roller Company ensures every roller is made from high-quality materials suited for its intended application, whether that involves withstanding harsh chemicals in a textile mill or enduring constant friction in a packaging plant. Looking for Long-Lasting Rubber Rollers? Choose Arvind Rub-Web Controls Ltd, your trusted Industrial Rubber Roller Manufacturer. We specialize in designing and delivering custom rollers engineered for strength, precision, and reliability. From nip rollers to printing and conveyor rollers, we provide tailored solutions to meet your specific industrial requirements. Longer Lifespan and Cost-Effectiveness It may seem counterintuitive, but spending a bit more upfront on high-quality rollers can actually save you money in the long run. High-quality rollers last longer, require less maintenance, and offer better resistance to environmental conditions. In the end? Less downtime, fewer replacements, and improved throughput. A reputable Rubber Roller Company invests in R&D, advanced production methods, and rigorous testing, so what you get is a roller that’s engineered for excellence and longevity. Poor-quality alternatives, while cheaper initially, tend to degrade quickly and underperform, especially in high-volume production setups. Customization Industries vary, and so do their roller requirements. General, off-the-shelf rollers may not always provide the best fit for your machines or processes. That’s why leading Rubber Roller Manufacturers offer customization options tailored to specific dimensions, materials, coatings, and hardness levels. Working with a knowledgeable Industrial Roller Company allows you to design rollers that align perfectly with your operational needs, whether it’s static elimination, ink transfer, pressure application, or heat resistance. customized rollers ensure seamless integration and optimized performance. Safety Another major aspect of choosing high-quality industrial rollers is safety. Certified rollers meet stringent quality and safety standards, ensuring they won’t fail under pressure, literally. Substandard rollers can not only harm machinery but also create safety risks for operators, leading to costly downtime and potential workplace hazards. Established Rubber Roller Manufacturers follow with global manufacturing standards and ensure their products pass endurance tests, dimensional accuracy checks, and chemical resistance evaluations. This level of conformance provides plant managers with peace of mind, ensuring both worker safety and uninterrupted production. Advanced Technology Modern Rubber Roller Manufacturers are continually creating by integrating advanced technologies into their production processes. Accurate engineering techniques such as CNC machining, balanced core construction, and advanced rubber compounding ensure that rollers not only meet but exceed industry standards. These technological advancements lead to smoother operation, reduced vibration, and lower energy consumption, ultimately boosting overall operational productivity. Investing in rollers manufactured with advanced technology means fewer mechanical issues, improved product quality, and longer service life, making it a smart choice for businesses to stay competitive in industry.1 Conclusion Industrial rollers may seem like minor components in the big machinery, but their impact is anything but small. From ensuring consistent results to enhancing equipment life, quality rollers are indispensable in industrial applications. That’s why it’s important to work with a trusted Industrial Roller Company that prioritizes quality, customization, and customer satisfaction. Don’t let substandard rollers slow you down. Choose durability, precision, and performance, choose a partner who understands your industry inside and out.
How to Choose the Right Rubber Rollers for Your Needs

Rubber Rollers play a primary role in many industrial applications, from printing and laminating to packaging and textile manufacturing. Choosing the right rubber rollers for your specific requirements can necessarily improve performance, product quality, and operational performance. At Arvind Rubber, a trusted rubber roller manufacturer, we understand the importance of selecting rollers that align with your application needs. Here’s a quick guide to help you make the right choice for your industrial operation. 1. Understand Your Needs : The first step in selecting a rubber roller is to understand your application. Are you using the roller for printing, coating, embossing, or conveying? Each use requires a different roller property. For example, printing rollers need accurate and high resistance to solvents, while conveyor rollers focus more on performance and high load capacity. 2. Select the Right Rubber Material Rubber rollers are available in various elastomers, each suited for different environments: At Arvind Rubber, we offer a large range of rubber compounds customized for industry-specific operational requirements. 3. Consider Roller Hardness The hardness of the rubber (measured in Shore A) determines how the roller will perform under pressure. Softer rollers (30-50 Shore A) are typically used in applications needing more grip, such as laminating. Harder rollers (70-90 Shore A) are suitable for high-speed operations or accurate tasks where less deformation is primary. 4. Check for Chemical and Temperature Resistance Ensure the rubber compound can withstand the chemicals and temperatures involved in your process. Failing to choose the right material may lead to premature wear, swelling, or cracking of the roller. 5. Roller range and Material Quality Besides the rubber compound, the core material (aluminum, steel, or composite) also affects performance. Steel mainly offers strength and longevity for heavy-duty industrial applications, while aluminum is the best choice for lightweight industrial operational needs. Make sure the roller diameter, length, and dimensions match your machine specifications requirements. 6. Work with an Experience Manufacturer Partnering with an experienced and well-known manufacturer like Arvind Rubber they ensure quality, customization, and performance. With many years of experience, we offer customized solutions for multiple industrial sectors, including printing, packaging, textiles, and more industries. Need help selecting the perfect rubber roller? Get in touch with the experts at Arvind Rubber for customized solutions that meet your exact requirements.
What are the ways to clean Rubber Rollers? How to prolong the durability of Rubber Roller?

Over the years technology has been at the driver’s seat in a wide gamut of industries, including industrial Rubber Rollers. Technology-driven companies are way ahead of their competitors, adapting modern technologies they reap substantial benefits from the technology executed. The Rubber Roller manufacturing companies aren’t lagging behind. In fact, many of them are harnessing the technology to scale up their production cycle and manage myriad processes seamlessly. Before shifting gears to the pivotal subject, let’s strive to comprehend the Rubber Roller in short! Understanding the Rubber Roller Industrial Rubber Rollers are being capitalized for different functions in manufacturing processes, including embossing machines, graphic art, laminating machines, offset printing, spreader, and laminator among others. Moving on to the manufacturing industries leveraging the roller, these include paper industry, plastic industry, textile mills, tyre, and lamination among others. The industrial Rubber Roller is a sophisticated product crafted with precision using modern tools and technology. In layman’s language, it’s an elastic material covering the core which is made up of metal or any other material. Why clean the Rubber Roller? Regular maintenance and cleaning of the product optimize durability. Being a businessman you are familiar with the significance of durability for a company. Increased durability directly impacts the growth of the company. A substantial amount of money could be saved merely through proper maintenance of the product. Well, look no further, let’s now move on to the pivotal subject – how to prolong the durability of Rubber Roller? Optimizing the durability of Rubber Rollers Cleaning and wiping: Instill this habit among the workforce, clean and wipe the roller at the end of the day on regular basis. This simple yet powerful habit would facilitate in eliminating unwarranted dust and dirt. Several industrial roller companies in India have integrated this process at their manufacturing facility. Before cleaning the roller, make sure you hold basic knowledge of the rubber compound, surface, and hardness. Otherwise, what will happen, certain chemicals might wreak havoc on the rubber surface. Your vendor can help you out with impeccable information. High temperature is dangerous High temperature and rubber are arch-rivals. Exposure of the product to high temperature damages its durability. Heating also impacts durability as bonding adhesive is vulnerable to high temperature and heat. Storing Every roller has a designated model to store it properly. Deviation from the standard process could severely damage the life span of the product. You don’t have to go overboard to prolong the life of the roller. So, how to store the roller? Many Manufacturers in India offer leaflets with clear instructions on storage. Hold the shaft and stand the roller upright, reason is – protect the rubber from coming in contact with damaging external material. Avoid UV radiation Exposure to UV radiation is harmful to rubber rollers. That’s why you are instructed to store your company’s valuable business asset in a dark place. Maintenance check Be meticulous during maintenance check of rubber rollers. Means? While inspecting a rubber roller, note down worn-out and damaged parts, like bearings, faulty gears, imbalanced rollers, etc. In case worn-out parts are remediable, get these repaired without a wait. Else, you can replace faulty parts with new ones. Maintenance isn’t rocket science; however, a comprehensive and structural policy is required at the workplace to imbibe the practice among the workers engaged in the operation. Besides, you can also roll out a regular inspection policy with crystal clear accountability. No point in executing a policy, if it’s not being adhered to in letter and spirit. Summary Industrial Rubber Rollers as suggested require regular maintenance and upkeep. It’s in the interest of the industry too? Why? Adherence to maintenance leads to optimal performance and durability.
Describe how industrial rubber rollers are manufactured
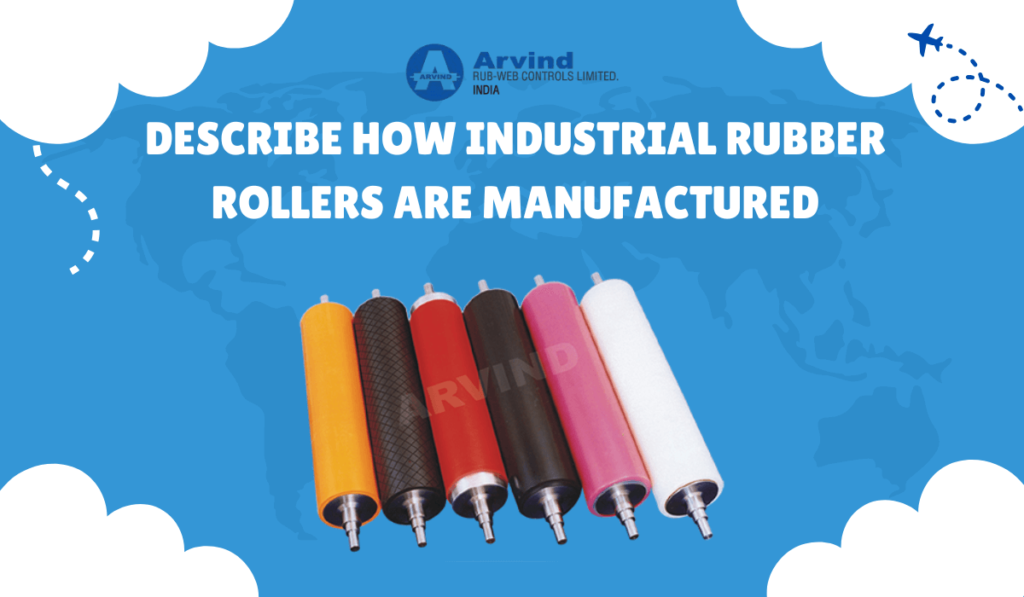
Over the years, rubber rollers manufacturing process technology has evolved substantially. Manufacturing companies across the globe, including India, are adapting new tools and technology to fabricate business-centric range enabling companies to materialize their business objectives. Redundant technology and processes are in fact swiftly fading away from the market. Rightly so! Obsolete methods increases production cost. In this short blog, we are going to highlight the manufacturing process, how industrial rollers are manufactured using modern tools and technology. Manufacturing process Industry experts have defined the manufacturing process in five stages: Preparation of Core and Rubber to Metal bonding A flawless adhesion between rubber and core is important as it plays a significant role in optimizing performance of rubber rolls in different industries. The process begins by exposing the cores to steam at about 150°C for numerous hours. This keeps anticorrosive materials applied on new cores at bay. When such similar processes are over, the cores are exposed to sandblast. It produces a unique metal surface, absolutely free from rust and dust. Using solvent, the cores are washed to ensure that it’s free from any grease or oil trace. In the form of a thin film, chemical bonding agents are applied evenly using a brush. The moment the film of bonding agent has dried, commence the buildup of the roll. Formation of Rubber Covering The first step is followed by the formation of a rubber covering. The rubber cover compound measuring 1.0-1.5 mm thick goes through cooling process with the support of cooling drums. Later on it’s wound with a polyethylene sheet. Now it’s time to apply a cover sheet over the core with the help of hand rollers. In many situations, use of extruded sheeting is preferred over calendered sheeting. There are reasons supporting it. Because the sheet doesn’t reflect any kind of blisters. These blister-free sheets can be of higher thickness (range of 4-8 mm). Such a feature reduces building time. Besides, there are a few other methods for the formation of rubber covering. Vulcanization Under the vulcanization process, crosslinks are created between the elastomer chains or the rubber compound. This process lends the polymer its necessary physical properties. The process of vulcanization is carried out by introducing the heat into the system. This supports the bonding of the curative agents, including sulfur and peroxide. Post heating process, the rubber is left to cure for a few hours. Later on, the rubber roller is cooled for the subsequent stage. Groove Cutting Under this process, specially designed grooved regions are created on the surface of the rubber roll. Subsequently, the surface area is expanded. The expanded area prevents slippage and improves heat dissipation. In addition, it is used for embossing and print patterns. Grinding Grinding process enables in smoothening the surface of the rubber cover as it wards off protruding parts. Besides, there also levels overlapping strips. The grinding process is carried out through a sophisticated machine called a grinding machine. The rubber rollers are rolled through an abrasive wheel, a kind of a turning lathe. Balancing is the last stage of the industrial roller company manufacturing rubber roller. There are two ways by which a roller can become imbalanced: static and dynamic. According to industry experts, static imbalance is identified when the roller rolls to its heavy side whenever allowed to rotate freely. Whereas a dynamic imbalance occurs when a rubber roll is rotated to its operating speed and generates vibration. Through testing the roller into a computer-monitored dynamic balancing system, dynamic balancing is addressed. Summary Taking into account various challenges and problems being faced by numerous industries, including packaging, textile, paper, plywood and laminate among others, the product is manufactured using innovative technology and processes.