Carbon Fiber Roller is all set to transform the packaging industry

In this era of changing market dynamics, innovation and discoveries are sprouting in abundance. Industry experts call it a golden age of evolution. Recall any sector, compare it with the decade-old technology, then you’ll realize, massive changes have taken place. Tools and technology have gone for a full spectrum change. Even the manufacturing sector hasn’t remained unaffected. Continued roll-out of innovative products and technology is facilitating in transforming the landscape of the manufacturing sector. In this specific blog, our effort is to expand your knowledge about an innovative product – Carbon Fiber Roller. What’s carbon fiber??? Understanding Carbon Fiber Before moving ahead, it’s pertinent to throw light on the game-changing carbon fiber. Carbon Fiber is one of the polymers, which comprises carbon atoms bonded together in the form of a chain. Owing to its unique properties, innovative carbon fibre is being leveraged in various sectors. Properties like Physical strength, specific toughness, lightweight, good vibration damping, high dimensional stability, low coefficient of thermal expansion, electrical conductivity, and resistance to corrosion among others lends it a unique identity. It’s five times stronger than steel and twice solid. Being a very strong and light material, it’s ideal for building a wide range of structures, including Carbon Fiber Roller. Owing to the unmatched properties of the product, it’s one of the most sought-after materials by engineers and designers! Fabricated using contemporary tools and technology, carbon fibre is identified with exemplary features, including about 8 to 10 times stronger than steel and aluminum, 75% lighter than steel, 30-35% lighter than aluminum. Significance of Carbon Fiber The unique Carbon Fiber is being employed for a wide range of applications. Experts have classified its use into two categories: a) In manufacturing specialized technology b) General engineering and transportation. Here are some of the uses of Carbon Fibre: Sporting goods: Golf shafts, tennis racquets, skis, snowboards, hockey sticks, fishing rods, bats, and bicycles. Transport: Aerospace (aircraft brakes, antenna, support structures, etc) road and marine. Electronic and Audio: Audio equipment, and loudspeakers for Hi-fi equipment, casings, and bases for electronic equipments. Healthcare: Medical applications in prostheses, surgery and x-ray equipment, implants, and tendon/ligament repair. Textile industry: Textile machinery, and general engineering. Chemical industry: Nuclear field, valves, seals, and pump components in process plants. Carbon Fiber Roller Since it’s an innovative product, not many companies in India are into the manufacturing of the industrial Carbon Fibre Roller. Modern technology and expert engineers are required to produce the Carbon Fiber Idler Rollers Carbon fiber is an ideal manufacturing material! Crafted adhering to stringent “Quality Policy”, the industry-centric innovative Carbon Fiber Roller is light in weight with low-inertia. Identical pivotal properties facilitate faster web speed, reduced vibration, and decreased waste. The durability of the product hugely impacts business progress. Carbon fiber is tailor-made for industries. Owing to better durability in comparison to steel and aluminum, it accelerates business progress. Why does the packaging industry employ Carbon Fiber Roller? Carbon fiber is among the latest addition to structural materials, used to craft a broad gamut of structures. However, its properties are exemplary, making it suitable for the manufacturing sector. Our range is crafted using impeccable raw material and complies with the industry benchmarks. Brilliant performance in a host of industries, including packaging demonstrates the competency of the Light Weight Carbon Fiber Rollers Unique Features Packaging industries across the globe rely on carbon fibre composite rollers for a wide range of applications, including Coater/laminator, Separator, Film, nonwoven cloth, and metal leaf, Slitter, Glass substrate treatment, and printer among others. Custom-designed Solutions Facilitated by the modern infrastructure and expertise of an astonishing team, a few manufacturers deliver custom-designed Carbon Fiber Roller. If you are looking for an expert to offer custom-designed solutions for your manufacturing company, then let’s connect with credible Carbon Fiber Composite Idler Rollers’ manufacturers, suppliers, and exporters. Summary The Carbon Fiber rollers are being looked upon as one of the gems of engineering as its unique features and various properties facilitate manufacturing industries to scale up. Rollers fabricated using the carbon fibre last longer. Owing to this unique feature, the company’s cost of maintenance reduces drastically. Another important feature, lighter in weight in comparison to steel and aluminum facilitates better tension control and swift response to any changes in the web. What else, as a businessman, you expect from the innovative product.
What is a rubber roller? How are rubber rollers manufactured?
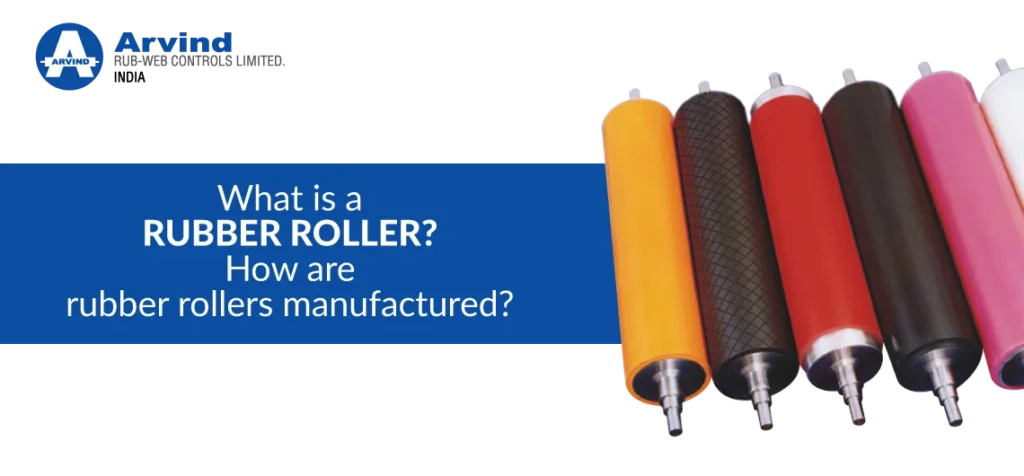
At the outset, it’s pivotal to understand Rubber Roller, before plunging into deep insight about the subject. The manufacturing sector is abuzz about the importance and impact created by the product. No point in making things cryptic. In this blog, we are going to focus on numerous indicators pertaining to the product. In layman’s language, a rubber roller is a sophisticated product comprising of an inner round shaft made up of metal, which is coated or covered by a designated compound elastomer or rubber. The inner shaft could be of different material, depends on industry requirements. Considering the current manufacturing landscape, the inner shaft is available in steel, aluminum, and carbon fiber. As far as the outer layer is concerned, it’s normally manufactured using polyurethane, silicone, EPDM, neoprene, and natural rubber. What’s so special about Industrial Rubber Rollers? There are definitely reasons galore behind employing rubber rollers in myriad manufacturing industries. Demonstrating unique properties associated with elastomers, including impact strength, shock absorption, tensile strength, abrasion resistance, high coefficient of friction, and controllable degree of hardness, the product enables a seamless business process. Similar unique features make them perfect for handling a wide gamut of manufactured goods, including textile, and food. The product assumes humongous significance for application wherein high surface durability with low to medium hardness is required. Besides, the product has the efficiency to withstand numerous degrading forces generated through mechanical and thermal factors. Applications Fabricated using state-of-the-art technology, the new age industrial rubber rollers are being employed to perform a wide range of applications. These include Printing, Film Processing, Material Conveying, Squeezing, Pressing, Laminating, Feeding, Spreading, Coating, Grains Milling, and wrinkle elimination among others. What are the benefits of using an industrial rubber roller Keeping in view the myriad challenges and benefits of the manufacturing industry, industrial rubber rollers are economical, and advantageous with brilliant mechanical properties. Moving forward, now let’s shift our attention towards another important subject pertaining to the industrial rollers – the manufacturing process. How to manufacture rubber rollers? The manufacturing process comprises a few sophisticated steps, including the fabrication of the roller core, rubber compounding, bonding, covering, vulcanizing, grinding, and balancing Roller Core Fabrication and Preparation Now, let’s move on to another significant part of this blog – the manufacturing process of industrial rubber rollers. Roller core fabrication process Employing the premium quality metal sheet, expert technicians, engineers, and welders fabricate a hollow tube. It’s executed through sheet rolling and welding. Flanges or support discs are cut according to the size and specifications to fit inside the cylinder. On the other hand, a shaft is manufactured using a lathe machine with the required cylindrical core. Dimensions and specifications should match the roundness and balance of the roller. Flanges fabricated at the beginning are welded to the ends of the cylinder along with the shaft. In order to make it resistant to corrosion and eliminate contaminants, it goes through secondary processes, including blasting and cleaning. Rubber Compounding As far as rubber compounding is concerned, it’s a formulation process wherein a few selected chemicals are added to the raw rubber. Why? The objective is to further strengthen its mechanical and chemical properties and support in processability and vulcanization. Some of the common compounding ingredients are filler systems (carbon black, silica, calcium carbonate), stabilizer systems (antioxidants, antiozonants), and vulcanizing agents (sulfur, peroxide). Bonding and building Bonding involves adhering the rubber layer/ cover to the roller’s surface using the premium quality adhesive or bonding agent or an ebonite layer. Post this process, the rubber building process begins. It comprises covering the rigid roller core with the rubber compound. Vulcanization and cooling It’s one of the significant processes followed by manufacturers to manufacture a wide range of rubber rollers, including Flexo Printing Rubber Roller. It’s employed to make the rubber more stable, facilitating it to resist the impact of solvents, heat, and cold. The process comprises creating crosslinks between the rubber compound. Crowning Under this process, the roller is shaped into different diameters along its length. It leads to a tapered, convex, or concave shape, such properties facilitate a slender deflection when pressed against a load. Groove cutting This sophisticated process helps in creating particular depressed and elevated regions on the roller’s surface. Such measures assist to prevent slippage, prevent heat dissipation, and to apply embossings and print patterns. Grinding The process of grinding smoothens the surface of the rubber layer. It eliminates protruding parts and leveling overlapping strips. Roller Core Balancing Leveraging the high-end computer-aided dynamic balancing system, rollers are evaluated, inspected, and corrected. Summary One of the most significant reasons behind using the rubber roller is its unique elastic features. On the contrary metal crafted rollers fail to offer any favourable elasticity. Metal isn’t resistant to corrosion, scratch, and dent. On the other hand, rollers made of other materials like fiber-reinforced composite aren’t easily available. Furthermore, fiber-reinforced composite rollers are expensive, scales production cost. Employing these wouldn’t be a wise business decision.
Unprecedented Carbon Fiber Airshaft redefines manufacturing
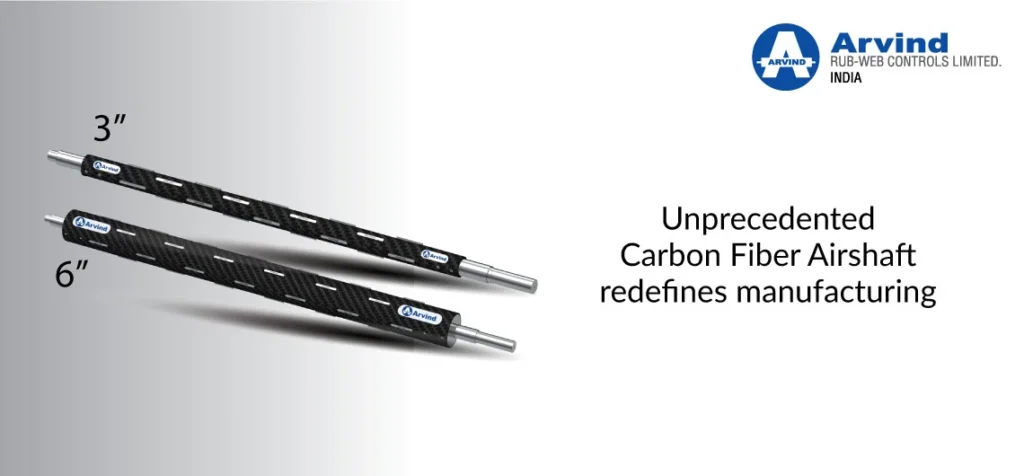
Ahmedabad, August 1, 2023: As an industry pioneer, Arvind Rub-Web Controls Ltd. continuously adapt to the market dynamics. Research and innovation are at the core of our business. The engineering phenomenon – Carbon Fiber Air Shaft is one of the latest additions to our ever-growing product portfolio. Owing to adherence to various quality parameters, including ultrasonic and impulse testing, the innovative range of Carbon Fiber Air Shaft provides optimized performance. Since it’s fabricated using high-strength carbon fibers, it’s ultra-light in weight, drastically reduces the time and man-hour required for core changeover. Packaging, paper, and plywood to name a few rely on the innovation driven Carbon Fiber Airshaft for various applications, including winding and unwinding. Rajanikant Patel, Chairman, and Managing Director, Arvind Group has termed the new product as “Unprecedented”. According to Mr. Patel, “the unprecedented Carbon Fiber Airshaft demonstrates our engineering competency and visionary approach. This product is going to transform the manufacturing sector allowing companies to scale up business at a rapid pace.” Manufacturing companies have been waiting since long for airshaft manufactured employing the unparalleled carbon fiber. The Carbon Fiber Air Shaft is another masterpiece of engineering from the industry pioneer! The unique Carbon Fiber industrial shaft is identified with numerous features and properties, these include strong and rigid design, lightweight, dimensional tolerance for better fitting, excellent grip for any core, and optimized performance among others. Here are a few unique features of the industry-centric product: Unique Features Specifications The engineering gem is tailor-made for Packaging, Paper, Plywood, Tyre, Steel, and Tape manufacturing industries among others. Adherence to global quality standards enables the shaft in performing a wide gamut of applications seamlessly, including winding and unwinding. Crafted using the state-of-the-art technology, the product is embedded with the competency to use in Rotogravure printing machine, Lamination machine, Slitting machine, Blown film plant, BOPP film plant, and pouch making process among others. About Arvind Rub-Web Controls Ltd. Driven by a visionary approach, Arvind Rub-Web Controls Ltd., the excellence focused company has established itself as an indisputable industry leader with several pioneering products to its credit. Backed by an unparalleled industry experience of four decades, over the years, we have thrived from the wealth of experience and boast of 100+ product range and presence in 52+ countries! For further information, connect with Nirav Patel, Director Email: director@arvindrubber.com Phone: +91-98795 36003 Website: https://arvindrubber.com/
Gems of engineering: Carbon Fiber Roller and Carbon Fiber Air Shaft scaling manufacturing sector
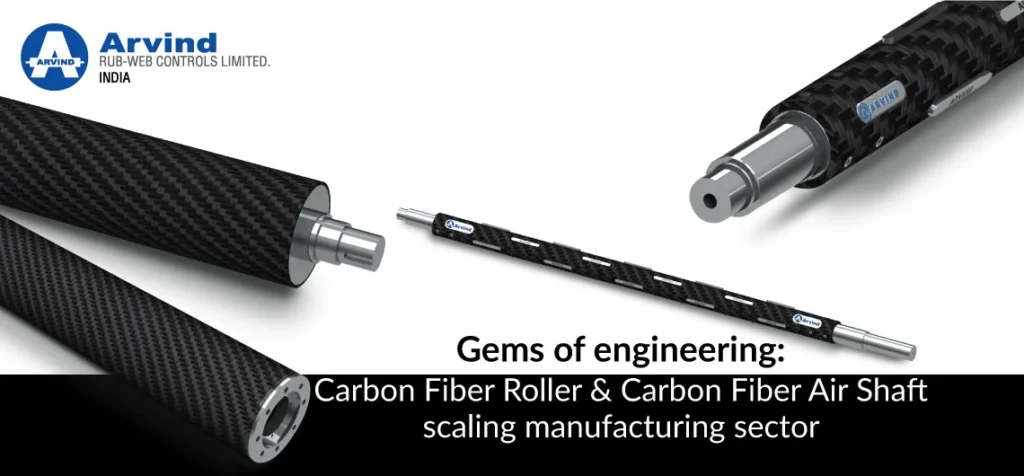
Ahmedabad, Aug 1, 2023: Driven by the rich legacy of four decades, Arvind Rub-Web Controls Ltd. is continuously making endeavours to roll out innovative products. Gems of engineering, Carbon Fiber Roller and Carbon Fiber Air Shaft further endorse the legacy of the company. Rajanikant Patel, Chairman, and Managing Director, Arvind Group has described the two products as a game-changer. According to Mr. Patel, “As an industry pioneer, we continuously adapt to the market dynamics. Research and innovation are at the core of our business. Innovative Carbon Fiber Roller and Carbon Fiber Air Shaft reflect our persistent endeavour to stay ahead of the industry.” Carbon Fiber Roller is an ideal product for the packaging industry, whereas Carbon Fiber Air Shaft is crafted keeping in view the industry requirements and challenges of Packaging, Paper, Plywood, Tyre, Steel, and Tape industries to name a few. Since the former is fabricated using high-strength carbon fibers, it’s ultra-light in weight, drastically reduces the time and man-hour required for core changeover, while the latter is identified with numerous features and properties, these include strong and rigid design, lightweight, dimensional tolerance for better fitting, excellent grip for any core, and optimized performance among others. Adherence to global quality standards enables the shaft in performing a wide gamut of applications seamlessly, including winding and unwinding. Crafted using state-of-the-art technology, the product is embedded with the competency to use in Rotogravure printing machine, Lamination machine, Slitting machine, Blown film plant, BOPP film plant, and pouch making process among others. Carbon fiber is among the latest addition to structural materials, used to craft a broad gamut of structures. However, its properties are exemplary, making it suitable for the manufacturing sector. Our range is crafted using impeccable raw material and complies with the industry benchmarks. Brilliant performance in a host of industries, including packaging demonstrates the competency of the Light Weight Carbon Fiber Rollers. About Arvind Rub-Web Controls Ltd. Driven by a visionary approach, Arvind Rub-Web Controls Ltd, the excellence focused company has established itself as an indisputable industry leader with several pioneering products to its credit. Backed by an unparalleled industry experience of four decades, over the years, we have thrived from the wealth of experience and boast of 100+ product range and presence in 52+ countries! For further information, connect with Nirav Patel, Director Email: director@arvindrubber.com Phone: +91-98795 36003 Website: https://arvindrubber.com/
What is a grinding machine? Describe its various functions briefly?
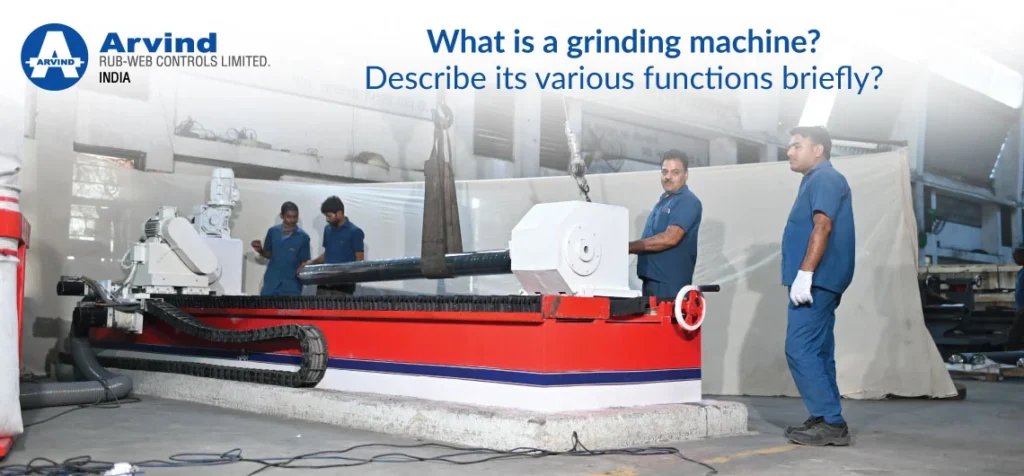
Over the years, industries cutting across domains are making endeavours to adapt new tools and technology in myriad processes. The reasons are obvious. Modern tools and technology facilitate optimized performance and in turn scale up the business operation. Ever-growing economic and manufacturing activities and surge in demand for brilliant surface quality is impacting the positive trajectory of grinding machines. Understanding the Grinding Machine Crafted using the latest technology, the large cylindrical grinding machine also known as a special-purpose grinding machine is a sophisticated tool used for grinding a wide range of large-scale heavy rollers. Besides, the modern machine is custom-made to grind convex, concave, and a host of other surfaces according to parabolic trajectory. Basics of the machine The grinding machine is embedded with an electric motor. The motor is meant to supply motion power to the grinding wheel with the help of a belt and pulley. As far as its movement is concerned – the moment the electric motor is switched on the motor rotates at a certain rpm assisted by v-belt and cone pulley, the grinding wheel too begins rotating. That’s the ideal position to begin various applications. Functions Depending on grinding processing, the grinding wheel can change metal or common grinding wheel. Moving on to grinding functions, the machine is competent to perform several grinding functions of roll shape, including Flat Grinding, Middle Convexity Grinding, Middle Concave Crown Grinding, Hammer Head Grinding, and Waveform Grinding. As far as groves are concerned, it performs different kinds of functions of processing – vertical groove, spiral groove, bhombus groove, man-shape groove and level groove on various kinds of roller shape respectively. Modern technology-enabled roll grinding machine, India can perform ideally in various challenging situations and is brilliant to make all the profiles of rollers. These could be, for instance, parabolic crowning and concave, cosine crowning and concave, circular, cone, coarse pitch, herringbone, diamond, straight groove, horizontal groove, and a host of many other formations. Roll Grinding Machine’s significance can be assumed from the fact that it can perform myriad processing schemes efficiently, these include cuttings, grindings, grooving, and combinations. Sounds exceptional! Yet, it has been made possible by modern technology. Salient features Specifications Packaging Industry Roll Grinding Machine Manufacturers offer a gamut of roll grinding machines, Specifications vary from manufacturer to manufacturer. Here are a few significant specifications pertaining to the machine being manufactured by a globally acclaimed Arvind Rub-Web Controls Ltd for the packaging industry: Textile Industry Using the latest technology, the innovative machine grinds out finished workpieces with immaculate surface quality and high accuracy dimensions. The specially designed machine gives optimal performance for all kinds of Textile rubber roller Grinding, Chambering (crowning), and Step Down processes. Precisely balanced Grinding Wheel and PLC controlled Servo Motors assist in grinding rubber roller. Application A range of applications, including step down & re-grinding of Rubber Roller & Quick Change Sleeve are performed seamlessly. Innovative design and easy-to-use mechanism enable the machine to provide optimal performance and in turn enable corporates in furthering their business! The specially crafted machine is custom-built for the packaging industry Industries leveraging the grinding machine The sophisticated grinding machine is being leveraged in a wide range of industries, including: Only procure a premium quality product There’s no dearth of Roll Grinding Machine Manufacturers in India. In fact the market is flooded with manufacturers offering a wide range of Roll Grinding Machine. However, don’t entice with the appearance of the machine. Being an entrepreneur, you must be acquainted with the pivotal role being played by the quality in scaling the growth of the company. Now an important question arises – how to establish quality. Well, checking quality isn’t rocket science. There are a few standard quality parameters, measure and inspect the quality on the basis of specifications engraved on the packaging, features claimed and mentioned by the manufacturer. Furthermore, what you can do is – Google credibility of the company, year of inception, headquarter, clients, etc. Summary Considering the challenges being encountered at the manufacturing facility by Roll Grinding Machine, it’s advisable to procure and install a premium quality machine.
What are the ways to clean Rubber Rollers? How to prolong the durability of Rubber Roller?

Over the years technology has been at the driver’s seat in a wide gamut of industries, including industrial Rubber Rollers. Technology-driven companies are way ahead of their competitors, adapting modern technologies they reap substantial benefits from the technology executed. The Rubber Roller manufacturing companies aren’t lagging behind. In fact, many of them are harnessing the technology to scale up their production cycle and manage myriad processes seamlessly. Before shifting gears to the pivotal subject, let’s strive to comprehend the Rubber Roller in short! Understanding the Rubber Roller Industrial Rubber Rollers are being capitalized for different functions in manufacturing processes, including embossing machines, graphic art, laminating machines, offset printing, spreader, and laminator among others. Moving on to the manufacturing industries leveraging the roller, these include paper industry, plastic industry, textile mills, tyre, and lamination among others. The industrial Rubber Roller is a sophisticated product crafted with precision using modern tools and technology. In layman’s language, it’s an elastic material covering the core which is made up of metal or any other material. Why clean the Rubber Roller? Regular maintenance and cleaning of the product optimize durability. Being a businessman you are familiar with the significance of durability for a company. Increased durability directly impacts the growth of the company. A substantial amount of money could be saved merely through proper maintenance of the product. Well, look no further, let’s now move on to the pivotal subject – how to prolong the durability of Rubber Roller? Optimizing the durability of Rubber Rollers Cleaning and wiping: Instill this habit among the workforce, clean and wipe the roller at the end of the day on regular basis. This simple yet powerful habit would facilitate in eliminating unwarranted dust and dirt. Several industrial roller companies in India have integrated this process at their manufacturing facility. Before cleaning the roller, make sure you hold basic knowledge of the rubber compound, surface, and hardness. Otherwise, what will happen, certain chemicals might wreak havoc on the rubber surface. Your vendor can help you out with impeccable information. High temperature is dangerous High temperature and rubber are arch-rivals. Exposure of the product to high temperature damages its durability. Heating also impacts durability as bonding adhesive is vulnerable to high temperature and heat. Storing Every roller has a designated model to store it properly. Deviation from the standard process could severely damage the life span of the product. You don’t have to go overboard to prolong the life of the roller. So, how to store the roller? Many Manufacturers in India offer leaflets with clear instructions on storage. Hold the shaft and stand the roller upright, reason is – protect the rubber from coming in contact with damaging external material. Avoid UV radiation Exposure to UV radiation is harmful to rubber rollers. That’s why you are instructed to store your company’s valuable business asset in a dark place. Maintenance check Be meticulous during maintenance check of rubber rollers. Means? While inspecting a rubber roller, note down worn-out and damaged parts, like bearings, faulty gears, imbalanced rollers, etc. In case worn-out parts are remediable, get these repaired without a wait. Else, you can replace faulty parts with new ones. Maintenance isn’t rocket science; however, a comprehensive and structural policy is required at the workplace to imbibe the practice among the workers engaged in the operation. Besides, you can also roll out a regular inspection policy with crystal clear accountability. No point in executing a policy, if it’s not being adhered to in letter and spirit. Summary Industrial Rubber Rollers as suggested require regular maintenance and upkeep. It’s in the interest of the industry too? Why? Adherence to maintenance leads to optimal performance and durability.
What is an Air Shaft? What are its applications in the manufacturing industry?

Over the years, technology has evolved extensively. Its impact can be observed in a wide range of manufacturing industries, including packaging, steel, paper, etc. Manufacturing processes are being redefined and redesigned leveraging the new age technology. Air Shaft, an integral part of a wide range of industries hasn’t remained unaffected. Before making a deep dive into the significant subject, let’s do Understanding Air Shaft As mentioned earlier, an Air Shaft is a mechanical device or machine integral to the manufacturing sector. The device is also known in the industry circles as “Air Mandrels”,”“Air Bars,” and “Air Expanding Shaft”. So, next time when your engineer friend asks you about Air Expanding Shaft, then don’t get puzzled by the name. It’s just another name for Air Shaft. The device is being used during the manufacturing process for fitting the core onto material surfaces, materials such as paper, card, and plastic film are wound there. Since being expandable, it’s embedded with swift and firm attachment features. Concurrently, during the process of fitting into a core, when the winding of the product gets completed, it’s ready for deflation function, which helps in easy removal of the shaft. An Air Shaft is tailor-made for handling winding reels in the processing of web-fed materials. Why does the Air Shaft called an Air Expanding Shaft? This is again an important question often raised. It’s high time to unravel the mystery. The reason is – on fitting into a core, due to design and functionality; the product can be easily expanded. As captured earlier, the device can be easily deflated in order to remove the shaft once the winding of the product is through. The technology-driven design has further lifted the efficiency, making them ideal for mounting onto bearing housings. It facilitates smooth winding and unwinding of rolls of stock material, at the same time minimum of equipment downtime. Types There are two types of Air Shaft: Lug Type Air Shaft:It contains an inflatable rubber tube inside. Multi Tube Air Shaft: It contains multiple bladders outside. Depending on their industrial requirements, industries can choose the Air Shaft. The expertise of a reputed Air Shaft Manufacturer can be leveraged while choosing your industry-centric product. Advantages of Air Shaft for manufacturing Before moving to advantages, here’s a pivotal reason to leverage the device. It’s efficient in griping the core, without causing any damage, at the same time lends a remarkable interface to control the web with the support of motors & brakes. As far as efficiency is concerned, it can be determined from the fact that the product is reliable to be used on a wide range of converting machines. Don’t assume that the description is a kind of glorification of the widely used product. A slitting machine or slitter rewinder is a classic example to depict the significance of the industrial product. Using the Air Shaft, the slitting machine fabricates large rolls of material into smaller rollers and pieces. The latest technology embeds a brilliant feature into the device, it’s efficient to amend according to speed variations and core widths. Features With the objective to make the product user-friendly, its design and operation have been kept uncomplicated. It doesn’t require a skilled person to operate. It’s easy to install. Design and material may vary from one Air Shaft Manufacturer to another. Custom-built designs A few Air Expanding Shaft, Manufacturers, India hold the expertise to offer a custom-built solution. Search engine support can be derived to reach out to experts offering custom-built designs. Summary Quality makes all the difference. Never negotiate with quality. While buying a product, ensure the credibility of the air shaft manufacturer.
What types of rubber rollers are used in woodworking manufacturing?
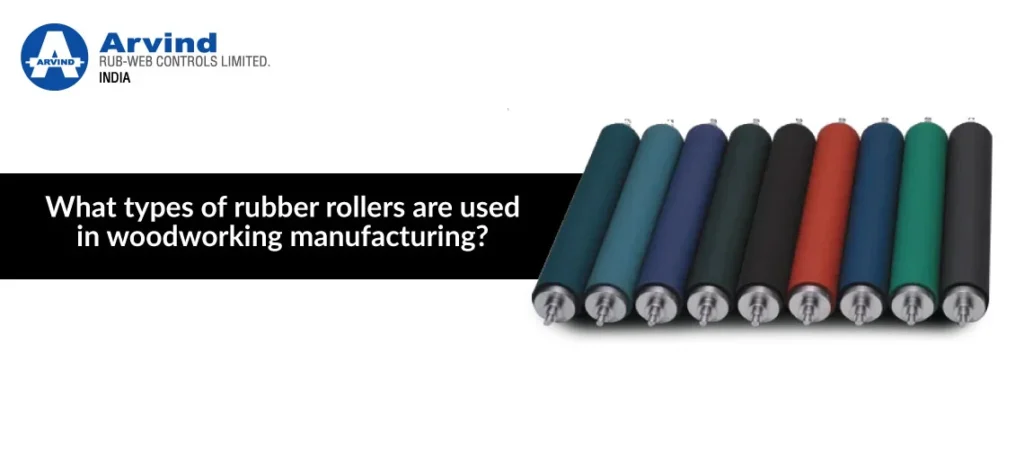
Continued innovation and technological developments have taken the industrial rollers’ industry by storm. Manufacturing industries using industrial rollers for a wide range of processes are capitalizing on evolving technology to scale their operation and accomplish business goals. Rightly so! There are reasons galore to validate and promote the dependency on modern technology. Outdated and redundant technology is like baggage. It starts gobbling cost-effective measures executed at your premises to cut down production costs. As a consequence, industry experts recommend continued streamlining of processes in line with the ever-changing market dynamics. For leading Rubber Roller Manufacturers, excellence is the key. And latest technology facilitates in deriving quality standards. Understanding woodworking industry In this brief write-up, we are highlighting the significance of rubber rollers in the woodworking industry. To begin with, let’s comprehend the basics of the woodworking industry. Woodworking in lay man’s language means, the skill of turning wood into furniture, handicraft, wood carving, household items (cabinets, doors, windows, etc.). Plywood and Laminate also fall under the broad umbrella of woodworking. Rubber Rollers in Plywood and Laminate Industries Considering a wide gamut of challenges being faced during manufacturing processes in Plywood and Laminate industries, Rubber Roller manufacturers have come out with a specific range of rollers. These rollers are industry-centric enable manufacturers to conduct business operations flawlessly. The Plywood industry-centric Rubber Rollers are: According to industry experts, Polyurethane Rollers are widely in demand in the wood industry sector as the rollers portray brilliant attributes. Here are a few attributes that make them appropriate for the industry: Quality parameters Rubber Rollers are at the core of manufacturing in the plywood and laminate industry. Quality assumes massive significance here. Poor or average quality wouldn’t suffice the business objective despite employing the best manpower. Consequently, you are recommended to lay emphasis on the quality of the Rubber Roller being used at your facility. Here are a few pointers to be evaluated while procuring and installing a rubber roller at your facility: Performance: The performance of the roller is directly proportional to the formulation of rubber chemicals. However, the foundation of the polymer remains the same. Finishing Precision: Dimensions and specifications must be in line with the design. Make sure, the product you are about to employ at your facility demonstrates flawless precision. Stable quality: The product should reflect stable strength, uniform hardness, pinholes, and no presence of external particles. Such measures facilitate smooth production and optimized durability. Roller Core Material and Structure: Make sure that the roller core material and structure are in line with the industry standards. The core is generally made up of steel or other robust material depends on the type of roller or client requirements. Proper Bonding: It’s again an intrinsic feature required in an industrial roller. Without excellent bonding, the rubber layer embedded might peel off. As an industrialist, you don’t expect that to happen to your roller. Unnecessary and avoidable hassle hampers business operations. Measuring the Hardness of the Rubber Roller In order to ensure the quality of the Rubber Roller, you can ask about Durometer. It’s pertinent to inform readers about this new age instrument. The Durometer is a globally recognized instrument employed to measure the hardness of rubber, an important layer. The instrument measures the hardness through the penetration process, by pressing an indenter into the rubber layer. We are sure, now you have an idea about the Durometer. Moving on to its unit, the hardness value is expressed in the form of plus or minus (+/-), for instance: 75+/- Durometer. Custom-built Rubber Rollers for Plywood and Laminate Industries A custom-built Rubber Roller is designed and manufactured considering the specifications provided by clients. Designing takes place after a comprehensive dialogue with the client. Features like dimensions, shape, size, colour, metal, etc., are taken into consideration. If you are looking for custom-built solutions for your industry, then render emphasis on quality. A casual approach could be disastrous for your business. Collaborate with a few leading Manufacturers, India. Don’t fall to branding blindly. Yes, that’s right. Many manufacturers sell ordinary products, however, their branding and marketing project them as unique. We recommend, don’t place the order based on the image created in the market. Perform comprehensive research, connect with a few of their clients, and then jump to any conclusion. Summary Quality makes all the difference! Consequently, while executing Rubber Rollers at your plywood or laminate facility ensure that the product range is of premium quality!
Understanding Industrial Quick Lock and its benefits

In this short blog, our focus will remain on quick lock. The engineering product looks like a precise metallic ring. However, it is not any kind of ordinary ring. It has found usage in numerous manufacturing industries. Over the years a combination of technology and engineering has defined its progress. The quality-focused range of Quick Locks has been acclaimed for excellent application at the rewind end as the tool provides brilliant gripping. Further, the tool is mechanically competent to demonstrate superior holding and high speed during operation. Benefits of the precision-driven tool The tool has been benefiting numerous industries with its application during a wide range of applications. Here are a few major benefits of the tool: Industries using quick lock The industrial tool has been used by various industries across every nook and corner of the country. Besides, it has found usage in the global market also. A few quick lock manufacturers in Gujarat, India are supplying products for the global market, including Europe and Middle-East. The industries that use the tool includes: Prominent features of the tool As a director of a plywood company wherein these kinds of tools has been used on large scale, your prime objective has been to procure a genuine tool. Otherwise, it will cast a shadow on the progress of the company. Consequently, quality assumes significance here. It is indeed important to focus on prominent features of the equipment, before making a final decision. Here are a few features a buyer should keep in view: Specification The dimension of the tool varies from company to company as it depends on the application. Here are a few standard dimensions of the tool: Sizes: 70 mm, 75mm, 100mm & 150mm Besides, custom-built sizes can also be delivered to meet the specific requirements of clients. However, not all manufacturing companies hold the competency to provide custom-designed solutions. Only a select few quick lock manufacturers, Ahmedabad, India hold the expertise! There is a range of industries, including packaging and plywood rely on the Core Saver for seamless application! Types of Quick Lock The engineering product comprises the following two types: Custom-made Many of you are well-versed with custom-made solutions. However, for a layman, the term is perhaps unheard. Any guesses? What is a custom-made solution? Why do a few companies claim it as their expertise? Here is the answer. Let’s unravel the mystery! Over the years, technology and engineering have evolved substantially, beyond belief. Subsequently, engineering companies have developed custom-made solutions. The research and development on the industry suggest that industry is witnessing an upward trajectory of custom-designed solutions corroborating its very impact. It’s a solution designed and developed keeping in view the requirements and dimensions of a particular project or company. What’s brilliant about this application is – it optimizes the efficiency and performance of a process wherein it is going to be commissioned. Similarly, a few functionalities that are unwarranted get knocked off. If your manufacturing industry requires a different set of dimensions. No worries. The custom-made solution providers are there to address your business requirements.
Describe how industrial rubber rollers are manufactured
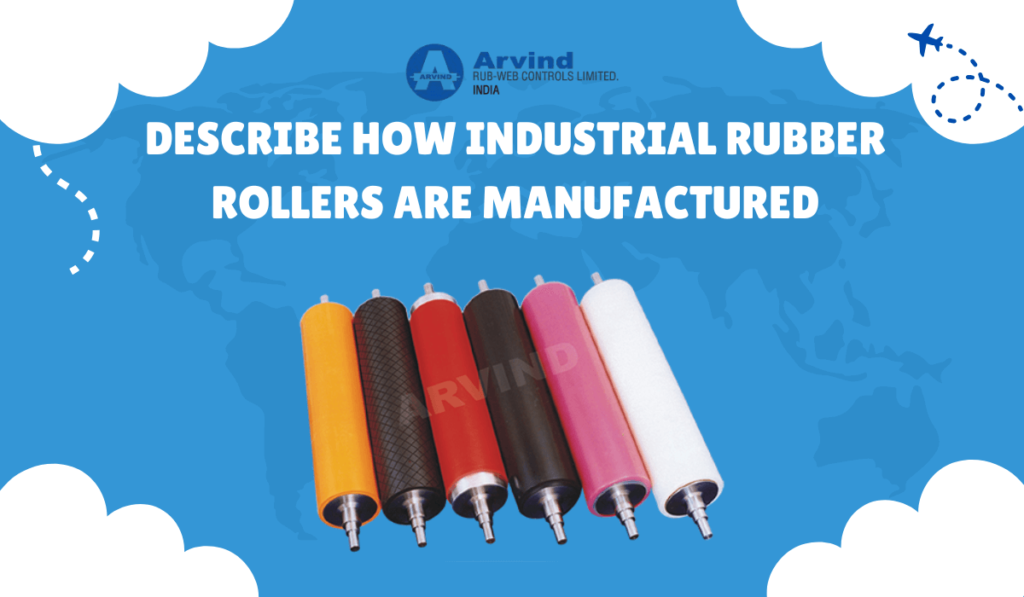
Over the years, rubber rollers manufacturing process technology has evolved substantially. Manufacturing companies across the globe, including India, are adapting new tools and technology to fabricate business-centric range enabling companies to materialize their business objectives. Redundant technology and processes are in fact swiftly fading away from the market. Rightly so! Obsolete methods increases production cost. In this short blog, we are going to highlight the manufacturing process, how industrial rollers are manufactured using modern tools and technology. Manufacturing process Industry experts have defined the manufacturing process in five stages: Preparation of Core and Rubber to Metal bonding A flawless adhesion between rubber and core is important as it plays a significant role in optimizing performance of rubber rolls in different industries. The process begins by exposing the cores to steam at about 150°C for numerous hours. This keeps anticorrosive materials applied on new cores at bay. When such similar processes are over, the cores are exposed to sandblast. It produces a unique metal surface, absolutely free from rust and dust. Using solvent, the cores are washed to ensure that it’s free from any grease or oil trace. In the form of a thin film, chemical bonding agents are applied evenly using a brush. The moment the film of bonding agent has dried, commence the buildup of the roll. Formation of Rubber Covering The first step is followed by the formation of a rubber covering. The rubber cover compound measuring 1.0-1.5 mm thick goes through cooling process with the support of cooling drums. Later on it’s wound with a polyethylene sheet. Now it’s time to apply a cover sheet over the core with the help of hand rollers. In many situations, use of extruded sheeting is preferred over calendered sheeting. There are reasons supporting it. Because the sheet doesn’t reflect any kind of blisters. These blister-free sheets can be of higher thickness (range of 4-8 mm). Such a feature reduces building time. Besides, there are a few other methods for the formation of rubber covering. Vulcanization Under the vulcanization process, crosslinks are created between the elastomer chains or the rubber compound. This process lends the polymer its necessary physical properties. The process of vulcanization is carried out by introducing the heat into the system. This supports the bonding of the curative agents, including sulfur and peroxide. Post heating process, the rubber is left to cure for a few hours. Later on, the rubber roller is cooled for the subsequent stage. Groove Cutting Under this process, specially designed grooved regions are created on the surface of the rubber roll. Subsequently, the surface area is expanded. The expanded area prevents slippage and improves heat dissipation. In addition, it is used for embossing and print patterns. Grinding Grinding process enables in smoothening the surface of the rubber cover as it wards off protruding parts. Besides, there also levels overlapping strips. The grinding process is carried out through a sophisticated machine called a grinding machine. The rubber rollers are rolled through an abrasive wheel, a kind of a turning lathe. Balancing is the last stage of the industrial roller company manufacturing rubber roller. There are two ways by which a roller can become imbalanced: static and dynamic. According to industry experts, static imbalance is identified when the roller rolls to its heavy side whenever allowed to rotate freely. Whereas a dynamic imbalance occurs when a rubber roll is rotated to its operating speed and generates vibration. Through testing the roller into a computer-monitored dynamic balancing system, dynamic balancing is addressed. Summary Taking into account various challenges and problems being faced by numerous industries, including packaging, textile, paper, plywood and laminate among others, the product is manufactured using innovative technology and processes.